详细说明
传统外墙粘贴式辅助保温作为“穿棉袄”式的补救性保温形式,在推广应用过程中出现了“畸形”发展,存在着以下主要弊病:
1)空鼓、开裂、渗水、脱落等质量问题严重,造成了众多“绷带”墙;
2)可燃性保温材料加无法全程监管的现实,使建筑火灾安全隐患突出;
3)外保温无法实现保温与建筑物同寿命,且二次维修的费用没有来源。
4)脱落时对居民人身财产的伤害隐患,砸车伤人事件时有发生;
5)脱落后的建筑垃圾无法有效处理,造成巨大的社会问题;
住建部2011年《“十二五”建筑节能专项规划》
到“十二五”末,城镇新建建筑执行不低于65%的节能标准,鼓励北京、山东等有条件的地区实施节能75%的节能标准。
七星实业公司突破传统,创新工艺、设备自动化程度高、实现闭环式循环生产:
1.储料和自动计量:实现精确计量,减少人工避免物料浪费,全封闭运行,减少环境污染;
2.PLC电脑控制混凝土下料系统:确保均匀布料,下料准确,实现产品密实,避免大气泡出现导致产品质量不稳定;
3.全自动生产线运行系统:
A、摩擦动力轮驱动,实现各个环节和工序的独立操控;
B、摩擦动力轮实现正反转,便于维修和故障排除,与传统汽缸硬顶的形式相比,摩擦动力轮实现软连接,避免破坏性生产事故;
C、自动限位与电控:实现各个模具的自动化运转;
D、链板输送机与升降平台:实现模块的自动摆渡,实现循环式紧凑性生产,使厂房利用更合理,大幅节省厂房空间,有效减少前期厂房投资;
4、生产线自动脱模系统:
A、精准定位:系统通过限位和电控以及机械定位系统,自动将模具传送至脱模系统;
B、整箱脱模:系统可以自动实现整箱36块脱模,一次性整箱脱模数量为行业内最大。
快速高效:
5、高位升降系统:高位升降系系统自动将切块叠成多层,转运到到切块养护车间,单位时间内实现更多切块运转,大幅提升运转效率;
6、自动清洗与覆膜系统
脱模后的磨具自动进入清洗流程,采用行业首创的用双排多头高压喷淋冲洗,全方位无死角,5秒清洗完毕;同时磨具底托自动覆膜,实现磨具底托免清洗化,减少人工投入、减少生产工序;
7、双排或多排整体保温芯体
行业首创一体化整体保温芯体,实现了芯体的精准定位,同时实现保温外壳与芯体的无缝连接,减少人工,提高效率。
8、自动多层预养系统
模具浇筑后自动进入预养仓,多层立体化的预养仓节省了大量的空间,实现一次性大批量砌块预养;
9、自然热能养护线
生产线厂房设计利用太阳光的力量进行自然养护,比传统蒸养形式大幅节省能源消耗,更有利于项目立项阶段的环评审批,复合发改委对于新型绿色建材的节能标准;
10、自动化程控多排转运车
转运速度快、操控性好,单次转运可以转运砌块3个立方以上,单次转运量为行业内最大;
11、自动化成品码垛系统
系统实现自动化5层码垛,提高了码垛效率,节省人工,便于成品快速运离厂房,提高生产效率。
12、底托自动电磁吸附转移系统
系统采用先进的电磁吸附技术,将底托自动吸附转运至生产线上,实现自动流水化循环生产;
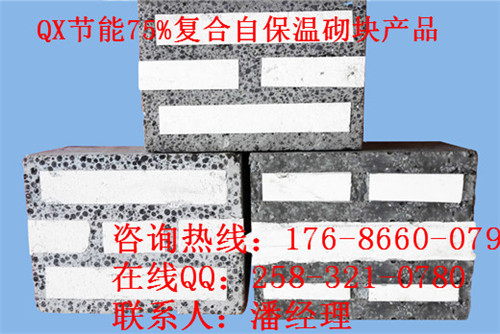
QX高性能复合自保温砌块采用全自动闭环式生产流程,采用模箱成型混凝土浇筑生产工艺,双排保温层先在模箱中定位,然后整体湿料浇筑高性能混凝土外壳,通过生产工艺使砌块壳体与保温材料注塑成整体而形成的集建筑围护与保温功能一体的混凝土自保温砌块。QX高性能混凝土复合自保温砌块采用断桥结构设计,可阻断和有效减小砌缝处热桥部位热量损失,梁、柱等热桥部位采用永久性复合保温板进行现场浇注成型,满足建筑节能75%及以上的建筑节能要求,实现了保温与结构同寿命的目的。